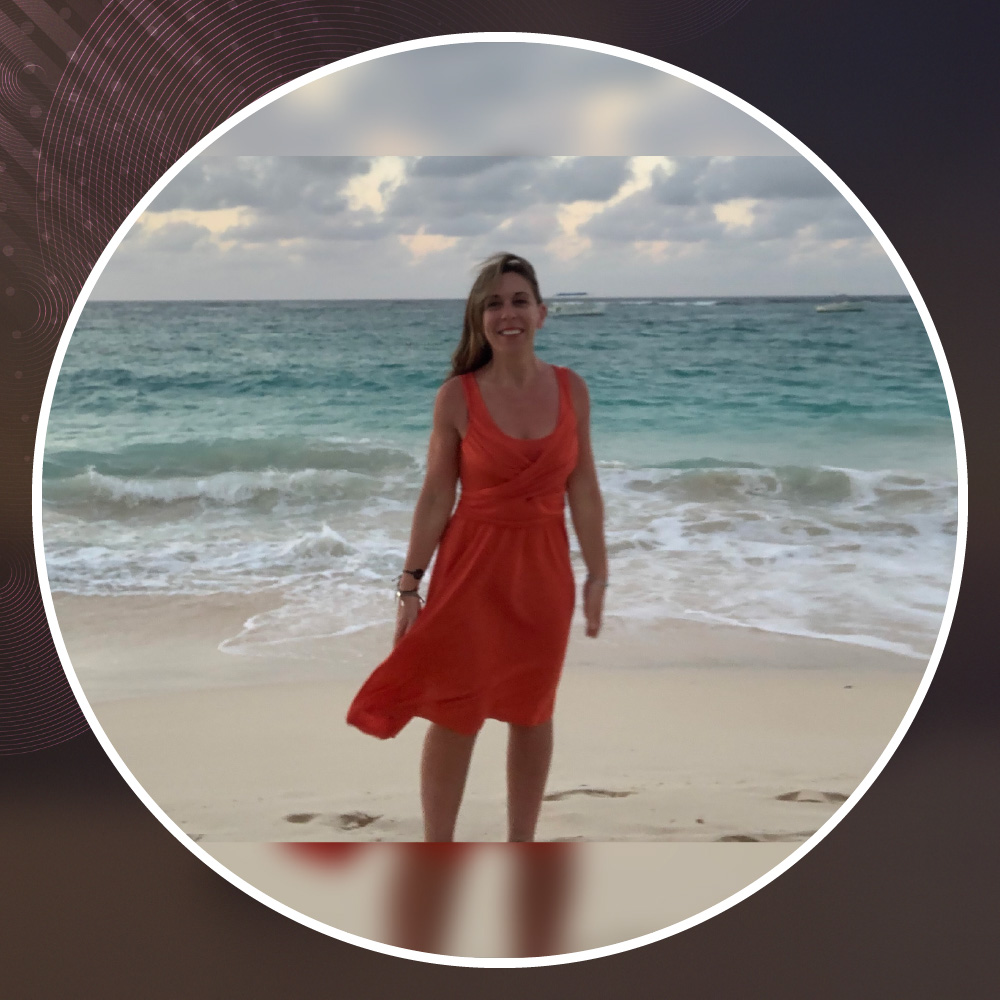
In the fast-paced business world, operational efficiency is critical to achieving sustainable growth and long-term success. Reducing costs while maintaining or improving productivity allows companies to stay competitive and reinvest in key areas for future expansion. By adopting targeted strategies that streamline operations, businesses can reduce waste, maximize resources, and improve overall performance. Here are key strategies for optimizing business operations to reduce costs and enhance efficiency.
Evaluate and Improve Workflow Processes
The first step to operational efficiency is thoroughly evaluating current workflows. Often, inefficiencies go unnoticed due to routine habits and legacy processes that no longer serve the business’s best interests. Mapping out each step of your workflows—whether in production, customer service, or internal communication—can reveal bottlenecks, redundant tasks, and unnecessary approvals that slow operations and waste resources.
After identifying inefficiencies, look for opportunities to improve processes by removing or simplifying unnecessary steps. Streamlined workflows should minimize manual interventions and increase automation where possible. Doing so reduces the time spent on repetitive tasks and frees employees to focus on higher-value activities. Continuous process improvement, guided by regular reviews, is key to maintaining operational agility and staying competitive in the market.
Automate Routine Tasks with Technology
Automating routine tasks is one of the most effective ways to reduce costs and improve efficiency. Manual processes such as data entry, invoicing, and inventory tracking consume significant time and increase the likelihood of human errors. Businesses can speed up these processes by leveraging automation tools while ensuring greater accuracy.
Investing in software solutions for accounting, customer relationship management (CRM), and enterprise resource planning (ERP) can greatly enhance productivity. These tools allow for automatic data handling, reducing the burden on employees and cutting operational costs. Automation also extends to marketing efforts, where scheduling social media posts, email campaigns, and customer follow-ups can be managed through platforms that ensure consistency and reduce manual effort. Ultimately, automation enables businesses to optimize operations, saving time and money.
Outsource Non-Essential Functions
Outsourcing non-essential functions is a powerful strategy for cutting costs without sacrificing quality. Tasks such as IT support, payroll, and customer service can often be handled more cost-effectively by specialized external providers. By outsourcing these functions, businesses can focus on their core activities while leaving non-core tasks to experts who can perform them efficiently.
In addition to cost savings, outsourcing brings flexibility to businesses by allowing them to scale services up or down based on demand without the burden of managing full-time staff. It also reduces overhead expenses related to hiring, training, and maintaining an in-house team for functions that do not directly contribute to the company’s primary mission. Outsourcing allows businesses to streamline operations while ensuring that essential services are delivered effectively.
Focus on Energy Efficiency and Resource Optimization
Operational efficiency is not limited to process improvements and automation—it also includes optimizing the physical resources the business uses. Energy consumption is often a significant cost driver, especially for companies with large office spaces, warehouses, or manufacturing facilities. Implementing energy-efficient solutions can have a substantial impact on cost reduction.
Upgrading to energy-efficient lighting, optimizing heating and cooling systems, and using smart building technology to regulate energy consumption are all strategies that can reduce overhead costs. Additionally, businesses should reduce waste in their supply chain and production processes. Lean manufacturing principles, such as just-in-time (JIT) inventory management, help minimize the costs associated with excess inventory, material waste, and overproduction. By optimizing energy and resource usage, businesses can enhance their environmental footprint while saving money.
Standardize and Document Procedures
Standardizing procedures across departments ensures tasks are completed consistently and efficiently. When employees follow different processes for the same task, it leads to confusion, delays, and errors that can drive up costs. By developing and implementing standard operating procedures (SOPs) for all routine tasks, businesses can ensure that employees have clear guidelines to follow, reducing the time spent on training and optimizing business operations mistakes.
Documenting these procedures also facilitates smoother onboarding of new employees and ensures continuity during transitions or staffing changes. Regularly reviewing and updating SOPs ensures they align with the latest technologies, industry standards, and business needs. A standardized approach not only improves efficiency but also enhances overall business performance.
Monitor and Measure Key Performance Indicators (KPIs)
To ensure the success of efforts to reduce costs and improve efficiency, Optimizing business operations need to monitor and measure key performance indicators (KPIs) regularly. KPIs such as production times, price per unit, profit margins, and customer satisfaction provide valuable insights into the business’s overall health. By tracking these metrics, companies can identify areas where operations lag and make data-driven decisions to improve them.
In addition to operational KPIs, financial metrics like cash flow, accounts payable, and return on investment (ROI) should be closely monitored. By monitoring financial performance closely, businesses can ensure they are operating within budget, managing resources efficiently, and identifying areas where cost savings can be realized. Regular reviews and adjustments based on KPIs ensure that businesses are constantly improving and staying ahead of challenges.
Optimizing business operations for cost reduction and efficiency is essential for long-term growth and profitability. Companies can significantly reduce expenses while improving productivity by evaluating workflows, leveraging automation, outsourcing non-core tasks, and implementing energy-efficient solutions. Standardizing processes and monitoring KPIs ensure that businesses maintain consistent operations and respond quickly to changing market conditions. By embracing these best practices, companies will be well-positioned to succeed in today’s competitive business environment.